A Comprehensive Guide to the Refine and Advantages of Plastic Extrusion
In the vast world of production, plastic extrusion emerges as a extremely effective and essential procedure. Transmuting raw plastic into continuous profiles, it provides to a myriad of industries with its remarkable adaptability.
Understanding the Basics of Plastic Extrusion
While it might show up facility at first glimpse, the procedure of plastic extrusion is fundamentally basic. The process begins with the feeding of plastic material, in the form of pellets, granules, or powders, into a warmed barrel. The designed plastic is after that cooled down, strengthened, and reduced into wanted sizes, completing the procedure.
The Technical Refine of Plastic Extrusion Explained
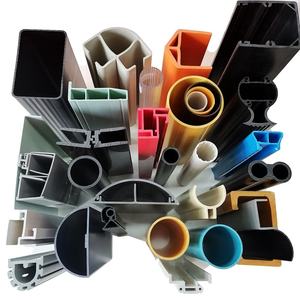
Sorts Of Plastic Suitable for Extrusion
The option of the right sort of plastic is an essential element of the extrusion procedure. Different plastics use one-of-a-kind homes, making them much more suited to specific applications. Polyethylene, for instance, is typically made use of due to its inexpensive and very easy formability. It uses exceptional resistance to chemicals and dampness, making it suitable for items like tubes and containers. In a similar way, polypropylene is an additional popular option due to its high melting point and resistance to fatigue. For even more durable applications, polystyrene and PVC (polyvinyl chloride) are often selected for their strength and longevity. Although these are usual choices, the selection ultimately depends upon the certain needs of the item being produced. So, recognizing these plastic types can considerably improve the extrusion procedure.
Contrasting Plastic Extrusion to Other Plastic Forming Approaches
Understanding the kinds of plastic appropriate for extrusion leads the way for a wider discussion on exactly how plastic extrusion stacks up against various other plastic creating approaches. These consist of shot molding, strike molding, and thermoforming. Each technique has its special uses and benefits. Injection molding, for circumstances, is outstanding for creating detailed parts, while strike molding is excellent for hollow objects like bottles. Thermoforming excels at developing superficial or large components. Plastic extrusion is unmatched when it comes to producing continual profiles, such as gaskets, pipes, and seals. It additionally permits for a consistent cross-section along the size of the product. Thus, the selection of method greatly depends upon the end-product needs and requirements.
Secret Benefits of Plastic Extrusion in Production
In the realm of manufacturing, plastic extrusion offers numerous considerable advantages. One noteworthy benefit is the cost-effectiveness of the process, which makes it a financially attractive manufacturing method. Additionally, this strategy provides superior item versatility and boosted manufacturing speed, thus enhancing total production effectiveness.
Cost-Effective Manufacturing Method
Plastic extrusion jumps to the center as an affordable production technique in production. In addition, plastic extrusion calls for much less power than typical production approaches, adding to lower functional expenses. On the whole, the financial benefits make plastic extrusion a highly attractive option in the manufacturing industry.
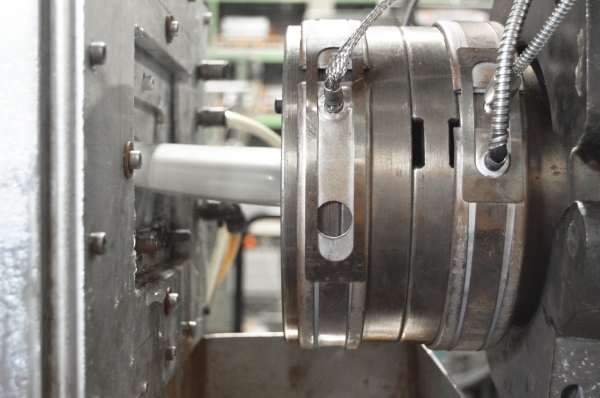
Superior Product Versatility
Beyond the cost-effectiveness of plastic extrusion, an additional substantial benefit in making lies in its remarkable product adaptability. This makes plastic extrusion a suitable solution for markets that need tailored plastic components, such click here to read as automobile, building and construction, and product packaging. In essence, plastic extrusion's product versatility cultivates innovation while enhancing operational effectiveness.
Boosted Manufacturing Rate
A considerable benefit of plastic extrusion lies in its boosted production speed. Couple of other production procedures can match the speed of plastic extrusion. In addition, the capability to maintain regular high-speed manufacturing without sacrificing item high quality sets plastic extrusion apart from various other techniques.
Real-world Applications and Influences of Plastic Extrusion
In the world of manufacturing, the strategy of plastic extrusion holds profound significance. This procedure visit this website is widely made browse this site use of in the production of a selection of products, such as plastic tubes, window structures, and weather condition stripping. Consequently, it significantly affects fields like building, product packaging, and vehicle industries. Its effect expands to everyday products, from plastic bags to tooth brushes and disposable flatware. The economic advantage of plastic extrusion, mainly its high-volume and economical output, has changed manufacturing. The environmental effect of plastic waste continues to be a concern. As a result, the industry is persistently pursuing technologies in naturally degradable and recyclable products, showing a future where the benefits of plastic extrusion can be kept without jeopardizing ecological sustainability.
Conclusion
To conclude, plastic extrusion is a very reliable and reliable method of transforming raw products right into varied products. It offers numerous benefits over various other plastic forming methods, consisting of cost-effectiveness, high outcome, minimal waste, and design adaptability. Its influence is exceptionally felt in numerous markets such as building, automotive, and durable goods, making it a pivotal procedure in today's production landscape.
Delving much deeper into the technological procedure of plastic extrusion, it begins with the option of the proper plastic material. As soon as cooled, the plastic is reduced into the required sizes or wound onto reels if the item is a plastic film or sheet - plastic extrusion. Contrasting Plastic Extrusion to Other Plastic Forming Approaches
Comprehending the types of plastic appropriate for extrusion paves the means for a broader conversation on exactly how plastic extrusion piles up against various other plastic developing approaches. Few various other manufacturing processes can match the speed of plastic extrusion.